Understanding Key Welding Standards for Butt Fusion Machines: ISO 21307 vs. DVS2207/1 vs. ASTM F2620
- Share
- Issue Time
- Mar 13,2025
Summary
Compare ISO 21307, DVS2207/1, and ASTM F2620 standards for HDPE pipe welding. Learn their differences, applications, and advantages for gas, water, and industrial projects.
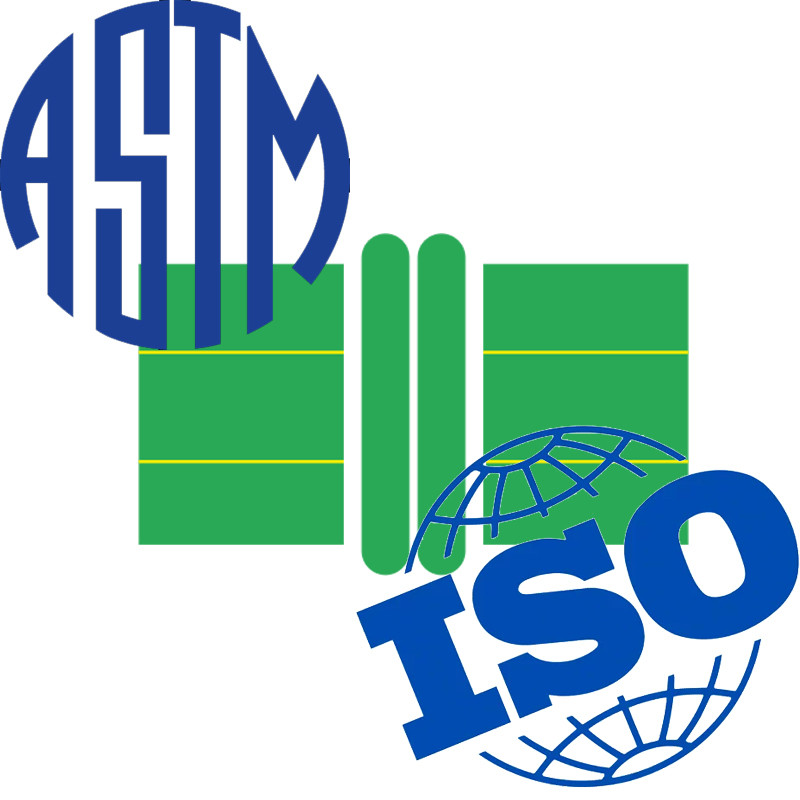
Introduction
Butt fusion welding is the backbone of modern HDPE pipeline systems, ensuring leak-proof joints for water, gas, and industrial applications. However, adherence to welding standards like ISO 21307, DVS2207/1, and ASTM F2620 is critical for compliance and performance. This blog dissects these standards, their unique requirements, and optimal use cases—equipping contractors and engineers with actionable insights.
1. ISO 21307: Global Compliance for Water & Gas Systems
Scope: Governs polyethylene (PE) pipe welding for water supply and gas distribution networks.
Key Requirements:
Temperature Control: Heating plate stability within ±3°C (e.g., 210–230°C for HDPE).
Pressure Phases: Mandates three-stage pressure application (alignment, fusion, cooling).
Data Logging: Recommends (but does not enforce) ISO 12176-4-compliant records.
Applications:
Municipal water projects (e.g., Mexico City’s pipeline renewal).
Gas pipelines requiring long-term durability under cyclic stress.
Advantages:
Global Acceptance: Preferred in Europe, Asia, and Latin America.
Flexibility: Accommodates DN50–DN1600 pipes.
Limitations:
Less stringent on real-time data tracking compared to ASTM.
2. DVS2207/1: Precision for Industrial & Chemical Pipelines
Scope: German standard emphasizing high-precision welds for chemical, mining, and industrial systems.
Key Requirements:
Surface Finish: Prohibits surface porosity >0.4t (material thickness).
Temperature Gradients: Heating plate surface temperature deviation <7°C.
Post-Weld Inspection: Mandates 10% cut-test sampling.
Applications:
Chemical plants using PVDF pipes (corrosion resistance).
Mining slurry pipelines requiring abrasion-resistant joints.
Advantages:
Strict Quality Control: Reduces weld defects by 60% in high-stress environments.
Material Versatility: Covers PE, PP, PVDF, and specialty polymers.
Limitations:
Complex documentation requirements increase project timelines.
3. ASTM F2620: North American Standard for High-Pressure Integrity
Scope: Focuses on gas pipelines and high-pressure systems in the U.S. and Canada.
Key Requirements:
Pressure Testing: 24-hour test at 2.5× maximum operating pressure (MAOP).
Hydraulic Precision: ±0.1MPa pressure control for DN200+ pipes.
Certification: Requires third-party validation for CE/ISO compliance.
Applications:
Offshore gas pipelines (e.g., Gulf Coast projects).
Industrial cooling systems with DR17 HDPE pipes.
Advantages:
Safety Assurance: 99.2% weld success rate in pressure tests.
Compatibility: Integrates with automated welders (e.g., servo-electric models).
Efficiency: Cooling time reduced greatly by 40%.
Limitations:
Higher equipment costs (e.g., hydraulic systems averaging $35k)
Comparative Analysis
Standard | Key Strength | Typical Use Case | Market Penetration |
ISO 21307 | Global adaptability | Municipal water networks | 65% EU/Asian projects |
DVS2207/1 | Industrial precision | Chemical/PVDF pipelines | 80% German industries |
ASTM F2620 | Pressure integrity | North American gas systems | 90% U.S. gas projects |
Choosing the Right Fusion Welding Standard
Project Type:
Water/Gas: ISO 21307 (budget-friendly, broad compatibility).
Industrial: DVS2207/1 (strict defect control).
High-Pressure: ASTM F2620 (safety-critical systems).
Regional Compliance:
EU projects often mandate ISO/DVS, while ASTM dominates North America.
Equipment Compatibility:
Machines like Riyang’s V630 support ISO 21307 low pressure and DVS2207/1.
Riyang’s V1200SHP HDPE fusion equipment meets ASTM F2620.
Conclusion
Understanding ISO 21307, DVS2207/1, and ASTM F2620 is pivotal for selecting the right butt fusion machine and ensuring project success. Whether installing water mains in Lima or gas pipelines in Texas, aligning with regional standards minimizes risks and maximizes ROI. For tailored solutions, explore Riyang solution for specific compliance needs.
RIYANG Fusion Manufacturing Limited, established in 2010, has emerged as a prominent force in the field of fusion welding equipment. Our journey began with a commitment to reliability, efficiency, and ruggedness. At RIYANG, our unwavering dedication to excellence is the cornerstone of our product design, engineering, and manufacturing. We take pride in offering advanced solutions to meet the evolving needs of the industry. For more information, please explore our RIYANG website at www.riyang-welding.com.