The Initial Settings of the Butt Fusion Machine
- Share
- Issue Time
- Dec 7,2021
Summary
This article will specifically share how to set the butt welder correctly, so as to help you connect the pipeline with the correct welding process parameters, ensuring the normal operation.
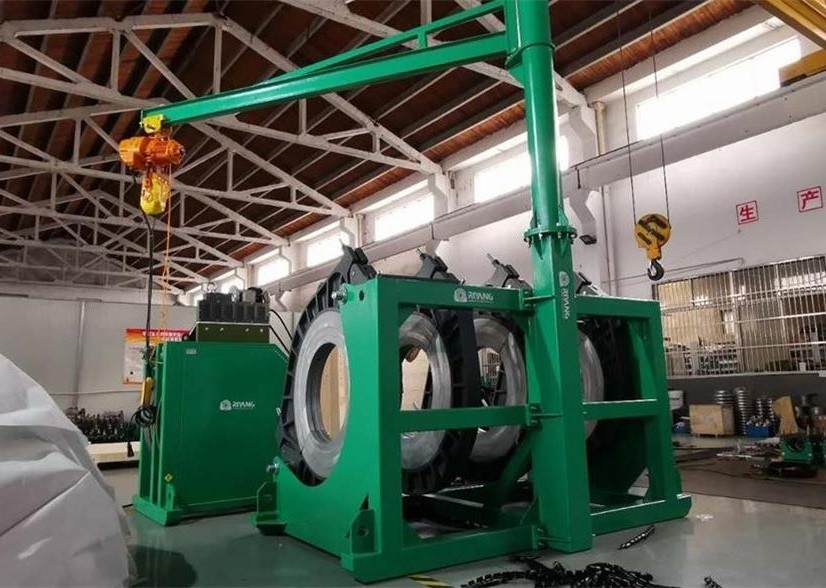
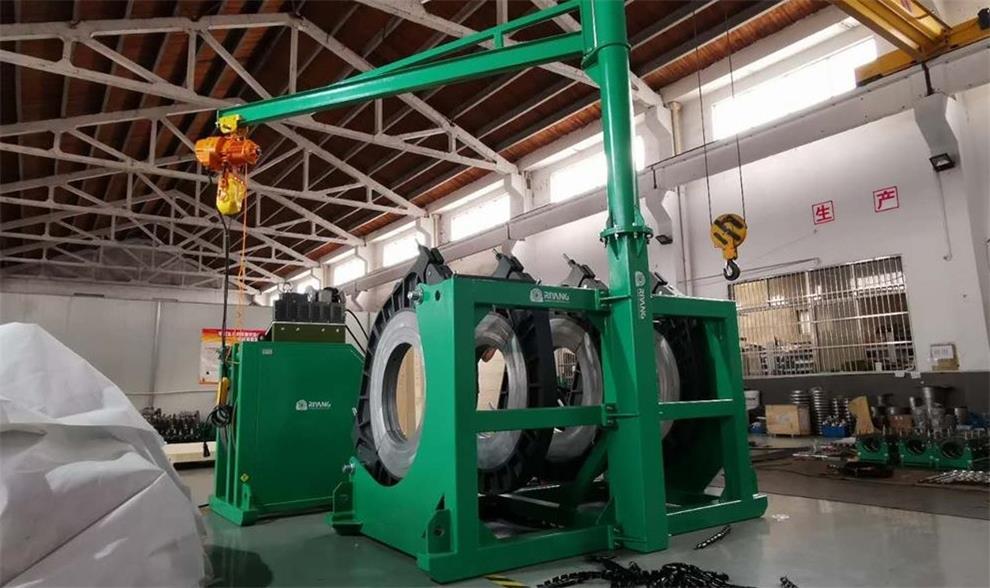
In the previous article, we shared the method of improving the butt welding machine in detail, but if we want the normal operation of the butt welding machine, we must correctly operate the initial settings. The followings are the specific steps and precautions about the initial settings of the butt fusion machine.
Positioning the Equipment
A butt welding machine is normally used inside a protective shelter, and not in an excavation. Deviations to this are allowed provided the basic principles we set out in the previous article are considered. A good location is preferably one on firm level ground where the butt welding machine can be anchored and pipe is free to move in and out of the machine without large drag forces as the butt weld is made.
A shelter is specified to reduce contamination risks in welding. This would include covering the ground beneath the machine to prevent vegetation or debris from being pulled up into the machine for example during the welding process. Also, roller supports are used for the pipe on either side of the butt welding machine to minimize drag forces during the welding process and to allow the pipe string to be advanced out of the machine once a weld is completed.
Power generation equipment should be located outside of the shelter to ensure any fumes from exhaust systems are vented to an area that allows for rapid dispersion to avoid risks to the health of the welder and their team.
Commissioning
Many countries in the European Community have legislation about the commissioning of machines in construction environments which should be adhered to. Butt welding machines normally have moving parts, electrical and hydraulic components that should be considered in this context.
It is normal to check electric cables are not damaged, nor are connectors and control units, to prevent the risk of electrocution of the welder. Hydraulic hoses and components are checked for leaking fluid or damage that might cause a burst hose, for example, to avoid injury and/or contamination of welds. Mechanical parts of the machine are checked to confirm the chassis is not bent, all parts move according to the manufacturer's intentions and where fitted, all guarding and emergency controls are functional.
When using the machine for the first time, there are two main considerations. That the heater plate is thoroughly cleaned, and that it achieves its working temperature across the area expected to be in contact with the pipe ends during welding. A good practice recommendation for this comes in the form of a 3 step process:
(1) Whilst it is cold, the heater plate can be taken from its protective sleeve and cleaned. Disposable single-use lint-free cloths are recommended for cleaning, together with isopropanol fluid if grease or oil contamination needs to be removed. Allow the plate to go back into and out of the protective sleeve a few times to make sure it is not recontaminated.
(2) The heater plate should be allowed to warm up to its working temperature which is usually in the range of 225 to 240℃. Once stable, manual measurements of its surface temperature are taken from both sides of the plate, around the full circumference expected to be in contact with the pipe ends, to confirm the plate temperature is correct.
(3) A final cleaning step is then recommended to remove any fine particles of dust or contamination which may be trapped in the hollows of the textured surface of the plate, a process known as making a dummy weld. To make a dummy weld, a normal weld procedure is followed but the cycle is aborted once the initial bead up phase is completed – at this point the molten pipe end is allowed to cool so that it can be machined again ready to make a full weld. For some larger pipes, it is often specified to make 2 dummy welds.
After installing the machine in the new location and debugging it in this way, we can make the first fusion welded joint, cut it after cooling, and send it for destructive testing. This means that the machine has been set up correctly and the supplied pipe is using the correct welding parameters.
For many years, RIYANG has been committed to the R&D, manufacturing, and sales of butt fusion machines. Our products line includes a butt fusion machine, HDPE pipe fitting machine, electrofusion machine, plastic sheet welding, socket fusion machine, pipe welding tools, etc. RIYANG butt fusion machine is known for its excellent engineering, ease of use, and ability to survive in the toughest conditions. At the same time, in order to allow users to have a good sense of experience, we also provide thoughtful one-stop service. If you are interested in our products, please contact us immediately!