Welding Data Logger Usage Guide
- Share
- Issue Time
- Mar 29,2022
Summary
A welding data logger refers to a system used to capture welding data during the welding process. The system is used as a data acquisition device as well as data to verify the welding process. It plays an important role in daily work, let's take a look at it.
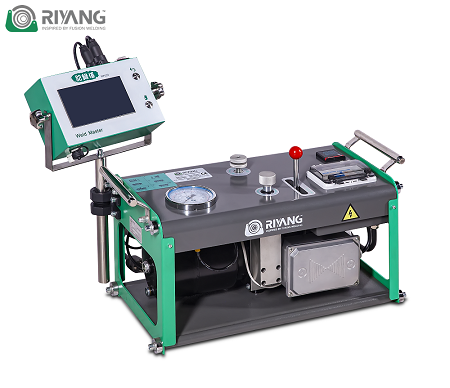
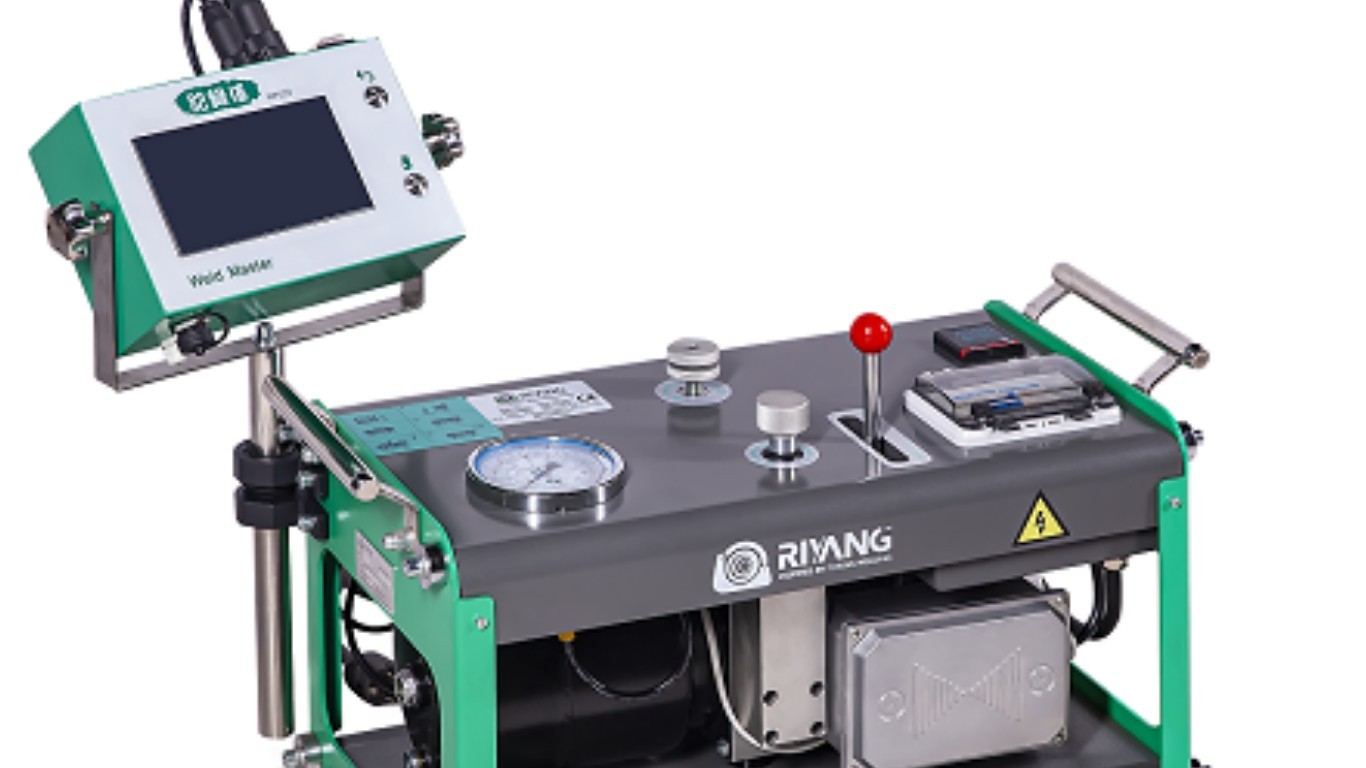
Welding data monitoring in arc welding
Welding data monitoring using a quality assurance system (QA system) is mainly used in automated welding systems for mass production or for welding tasks that require recording of welding parameters. Weld data monitoring also covers application areas not adequately covered by classical NDT processes and, in automated mass production, allows monitoring of all welds during production.
What is a welding data logger?
Welding data logger systems represent systems used to capture welding data during the welding process. Capture all essential parameters such as welding current, welding voltage, arc length, travel speed, and other essential variables using the system responsible for weld deposit quality. The system is used as a data acquisition device as well as data to verify the welding process.
Purpose of the data logger system
1. Measurement and display of quality-related parameters
2. Record and store signal curves
3. Determine the "Scope of Work"
4. Monitoring Limits for "Working Range"
5. Alerts when leaving the "scope of work"
6. Statement on the possible quality of the weld
7. Manufacturing Statistics
Measuring process parameters in resistance welding
Process heat during resistance welding is generated by the flow of current I through resistor R for a period of time t.
Voltage U and resistor R determine the current level. So current is a dependent parameter.
This correlation is expressed by the formula for the current thermal Q:
Q = I2 x R x t
The resistance R is a complex parameter that depends inter alia on the electrode force, the material, and it's surface quality (contact resistance).
Electrode geometry plays a more important role. Depending on the contact surface (convex surface), the current density increases or decreases.
Therefore, the following parameters are important for welding operations:
Welding current
Electrode force
Welding time
Contact resistance layer thickness
Electrode geometry.
Welding current in resistance welding
The levels, types, and frequencies of current in resistance welding cover a wide range. This ranges from a current level of 200A (micro-connection) to about 400kA (projection welding).
In AC current, the current type changes from pure sinusoidal current to sinusoidal current with a strong phase tangent.
In the DC power based on 50Hz commercial power, the selection of the transformer circuit and the diode rectifier circuit plays an important role in the ripple of the DC power.
Using an inverter current source produces a current with a high rate of change and low residual ripple.
To measure all these currents, magnetic voltmeters are mainly used. They are often called "pulse ammeters".
In daily work, data monitoring is of great significance. It can monitor the working data of the welding machine in real-time so that you can feel more at ease. If you have related needs, please contact us.
RIYANG is a thermoplastic welding machines manufacturer. Mainly produces butt fusion machine, plastic welding machine, electric fusion machine, etc. The RIYANG brand represents product reliability, pioneering innovation, accurate communication, and outstanding after-sales service. We are committed to the establishment of a successful community of production, design, service, and problem solver, all of which will be closely related to our global customers, partners, and employees. We will work on a better global infrastructure.