How to Choose the Best Plastic Welder?
- Share
- Issue Time
- May 31,2022
Summary
Plastic welders are used to joining thermoplastic materials together. The tool brings the plastic material to its specific welding temperature and then joins the parts under pressure. The following article details how to choose the best plastic welding machine.
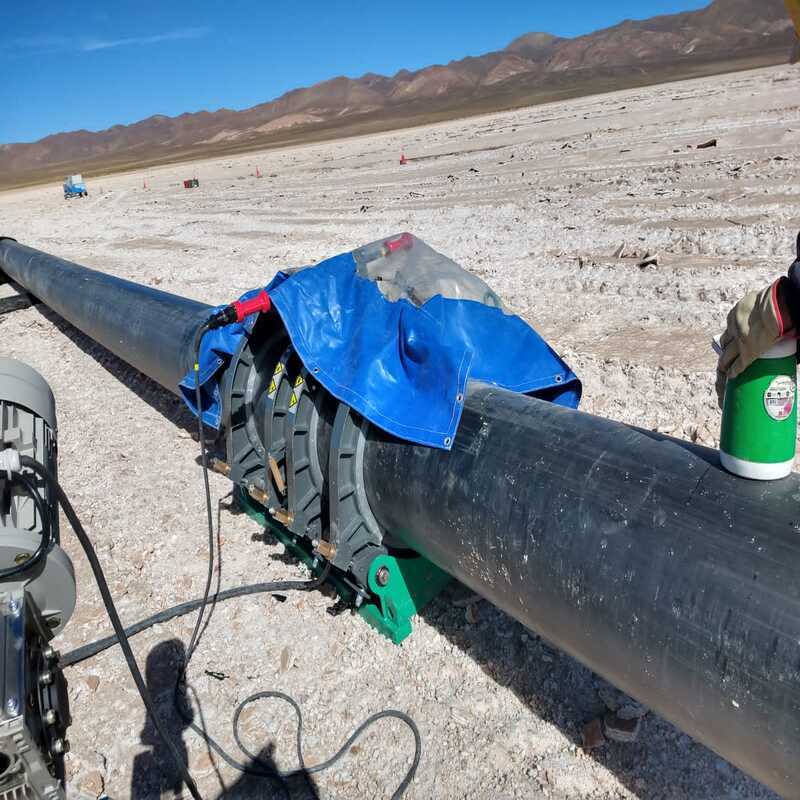
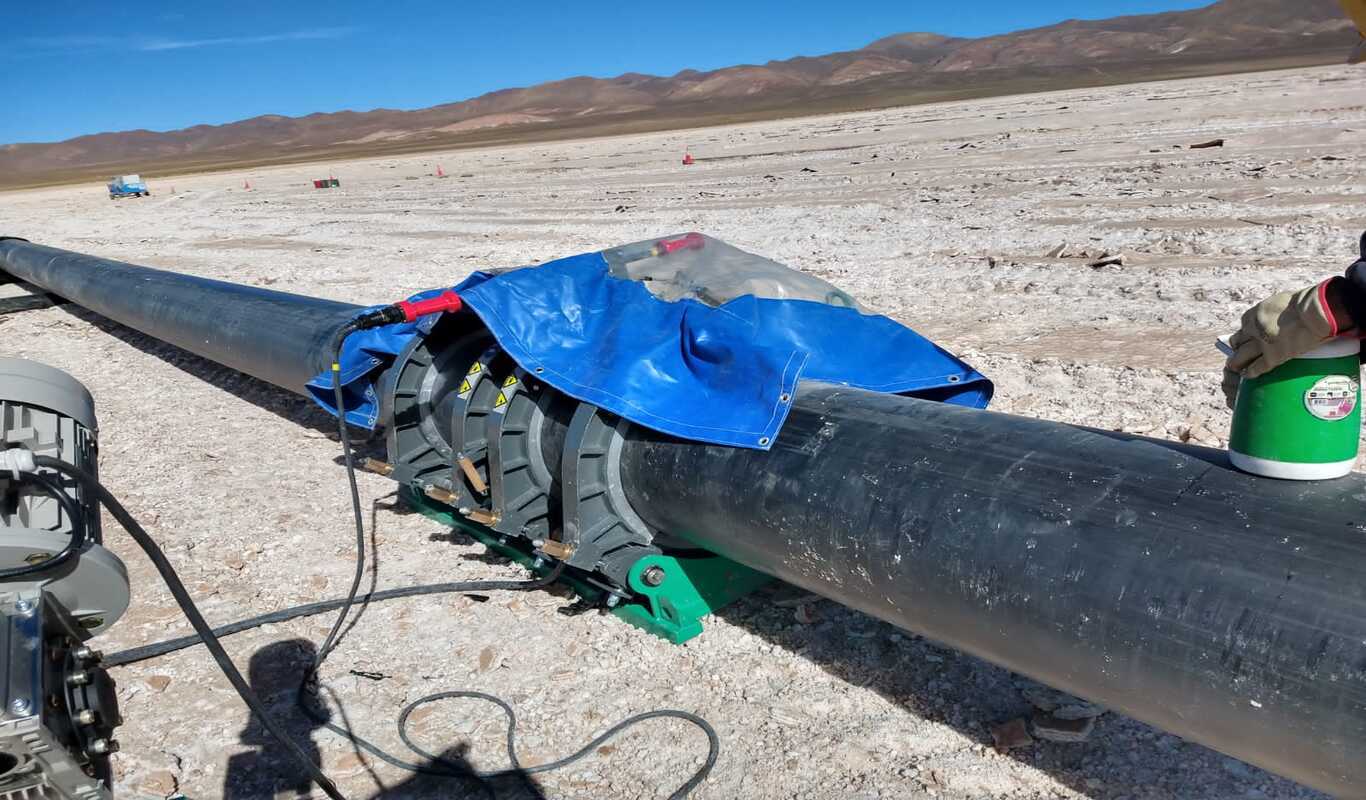
Plastic welders are used to joining thermoplastic materials together. The tool brings the plastic material to its specific welding temperature and then joins the parts under pressure. When choosing the best plastic welder, it's important to understand the different types of plastic welders, as each plastic requires a different method of joining.
Some welding machines are self-contained and easily portable; others require an air or gas source and are stationary units. Types of plastic welders include handheld "stick" welders, airless welders, extrusion welders, and injection welders. Knowing the application and the materials to be joined is the first step in choosing the best plastic welder for the job.
Identifying the plastic being welded is the key to achieving a strong bond. Identifying the type of plastic is as simple as looking at the identification number of the material itself. Another option is to use a testing lab to help identify plastic mixtures.
Often, the most accurate home test is the burn test; since each plastic produces a different odor when burned, burning the plastic helps identify the type. Once you have determined the type of plastic, you may want to keep a sample for future reference. It is also important to note that plastics can only be welded to similar plastics; that is, different types of plastics will not be welded together.
A handheld hot air welder or stick welder is a common portable plastic welder. They use a heat source to soften plastic while melting plastic rods to fill gaps. The key to getting a good bond from a stick welder is maintaining consistent down pressure, the distance between heat source and tool, and working speed. Features to look for in an electrode machine include a way to control the air pressure, preferably with a small portable compressor; some way to fine-tune the heat source - a heat source with multiple elements is a bonus; and interchangeable tips to choose the best-fit Shapes for plastic welding applications.
An airless plastic welder is similar to a stick welder but uses a heating element to melt smaller plastic rods without the use of heating the outside air supply. This type of plastic welder can often eliminate excess electrode buildup and help avoid panel warping. The final weld should typically penetrate about 75% of the substrate and should typically be allowed to air cool for at least 30 minutes.
The extrusion welder is larger than the first two units, so if space is an issue, this may not be for you. This plastic welder offers larger weld beads and is usually a floor-standing machine. The weight of the machine itself provides downward pressure during the welding process.
Injection welders are a lightweight and portable-a great choice if mobility is required. Generally, they are easy to use and produce high-quality bonds. The key to good welding with an injection welder is being able to change the aluminum tips on a plastic welder to suit the desired proportions.
The above describes the characteristics of different types of plastic welding machines in detail. If you want to know more or want to buy plastic welding machines, please contact us.
RIYANG is a professional custom plastic welding machines manufacturer, the RIYANG brand stands for product reliability, pioneering innovation, accurate communication, and excellent after-sales service. We are committed to building a successful community of production, design, service, and problem solvers, all of which will be closely related to our global customers, partners, and employees. We are committed to building better global infrastructure.