How to Do Proper Electrofusion Welding?
- Share
- Issue Time
- Jun 23,2022
Summary
The welding principle is the same in all cases; the surfaces to be welded are heated to a certain temperature, and then the surfaces are pressed against each other with a certain force to allow soaking and mixing, thereby melting. Below are the detailed steps for proper capacitor soldering.
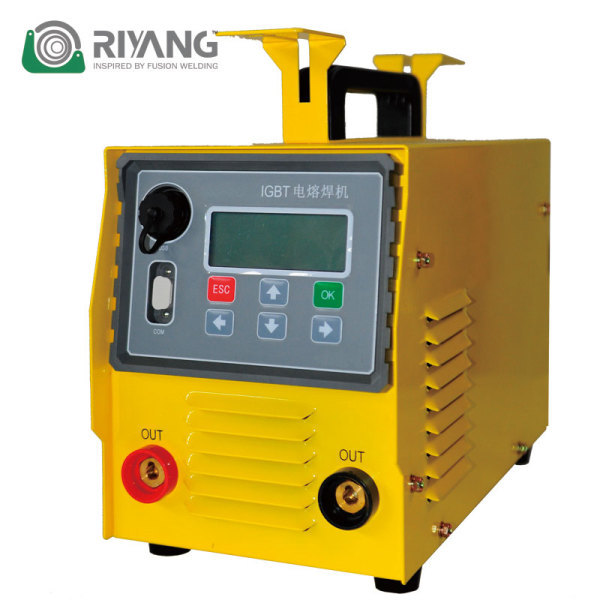
The welding principle is the same in all cases; the surface to be welded is heated to a certain temperature under the action of an electrofusion welding machine, such as placing polyethylene in a molten state, and then pressing the surfaces against each other with a certain force to Allow to soak and mix to melt. When the fusion procedure is performed according to the material manufacturer's instructions, the result is that the welded area becomes as strong, if not as strong, in mechanical resistance as the non-welded portion. When the welding area returns to near ambient temperature, the joint can be moved without risk of damage.
Proper preparation of components to be soldered
The basic procedure requires the execution of the following phases:
a) Prepare the components for welding: All traces of mud, dust, grease, or any other dirt on the inner and outer surfaces of the pipe affected by the welding. Cleaning must be done with water, then with a clean cordless rag or a soft paper towel moistened with a suitable liquid detergent;
b) Cutting the ends to be welded: they must be flat and perpendicular to their own axis; must be cut with a dedicated pipe cutter or equipment used with fixed guide blades; the outer edges of the ends must be deburred, to remove any polyethylene fragments and possibly bevel;
c) Mark the scratched area: Use the marker on at least one-third of the circumference of the pipe. The scraping length at each end must be at least 10mm greater than the coupling depth length of the electrofusion junction;
d) Removal of the oxidized surface layer: On the entire outer surface of the components to be soldered, the surface oxide layer must be removed using a suitable scraper, either manually or mechanically.
e) Cleaning the scraping surface: After scraping, the ends affected by welding must be cleaned again with a suitable cleaning agent. Make sure all surfaces are completely dry before moving on to the next stage. Cleaning operations with cleaning agents must also be performed on the inner surface of the electrofusion fitting (must be removed from its protective packaging before positioning on the pipe);
f) Mark the insertion depth: mark the insertion depth on at least one-third of the circumference of the two ends of the component to be welded with a marker; the depth must be equal to half the length of the fitting;
g) Insert the components to be welded into the electrofusion joint: the insertion must be carried out in a way that ensures the coaxiality of the components. Do not force any components into the fitting, if necessary, check for diameter and out-of-roundness. The markings indicating the depth of insertion previously marked on the element must be observed.
Welding period
After completing the illustrated stages, do the following:
a) Connect the terminal of the control unit (welding machine) to the electrofusion joint: check whether the diameters of the connecting terminal and the joint terminal are consistent, and transmit the welding parameters displayed in the joint barcode to the optical reader of the control unit by method, if everything is consistent, the welding cycle begins;
b) Mark the joint: write the hour and minute on the clock representing the end of the fusion time with a marker; mark the joint with its name (or abbreviation/code);
c) Wait for the entire cooldown period to elapse.
The above briefly introduces the correct electrofusion welding steps. If you want to know more or want to buy an electrofusion welding machine, please contact us.
RIYANG is a professional custom butt fusion machine manufacturer. We offer a wide range of products to meet the needs of field and workshop projects. Our products operate all over the world due to reliability, creativity, and cost-effectiveness. At RIYANG, we are committed to making reliable machines for every application and making sure your choice is the right one.
FORCEMAX30-8K is a connecting device used for polythene pressure and non-pressure pipe electrofusion or socket connection.