Pipe Fusion Machine Selection Guide
- Share
- Issue Time
- Jul 5,2022
Summary
Pipe fusion machines weld plastic pipes and fittings. These machines are used to prepare and join thermoplastic polymer materials. The fusion splicer heats the ends of pipes and fittings and presses them together to form a pressure-tight, uniform joint, and creating a continuous piping system.
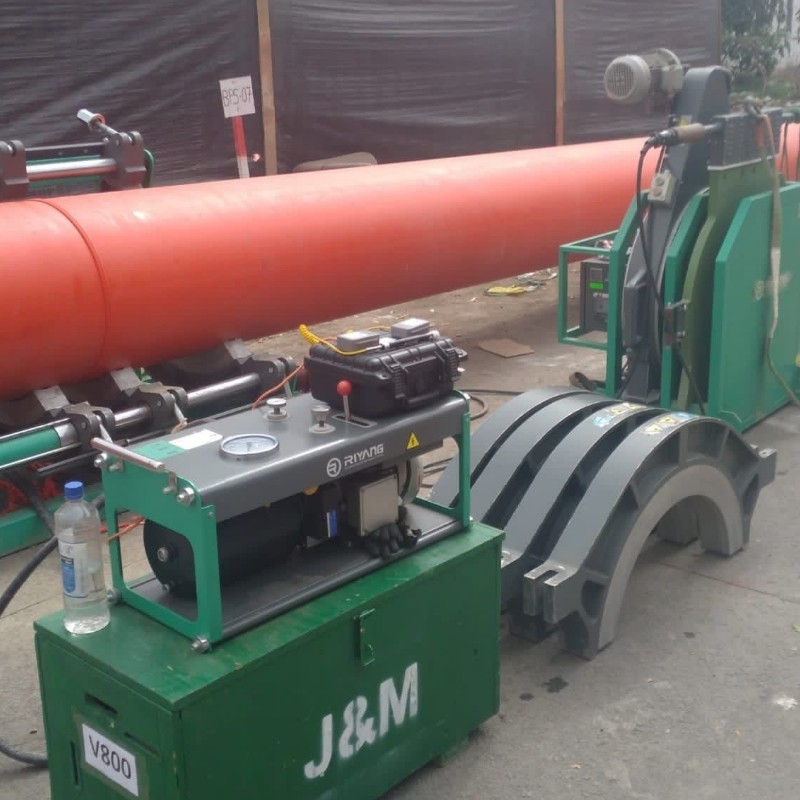
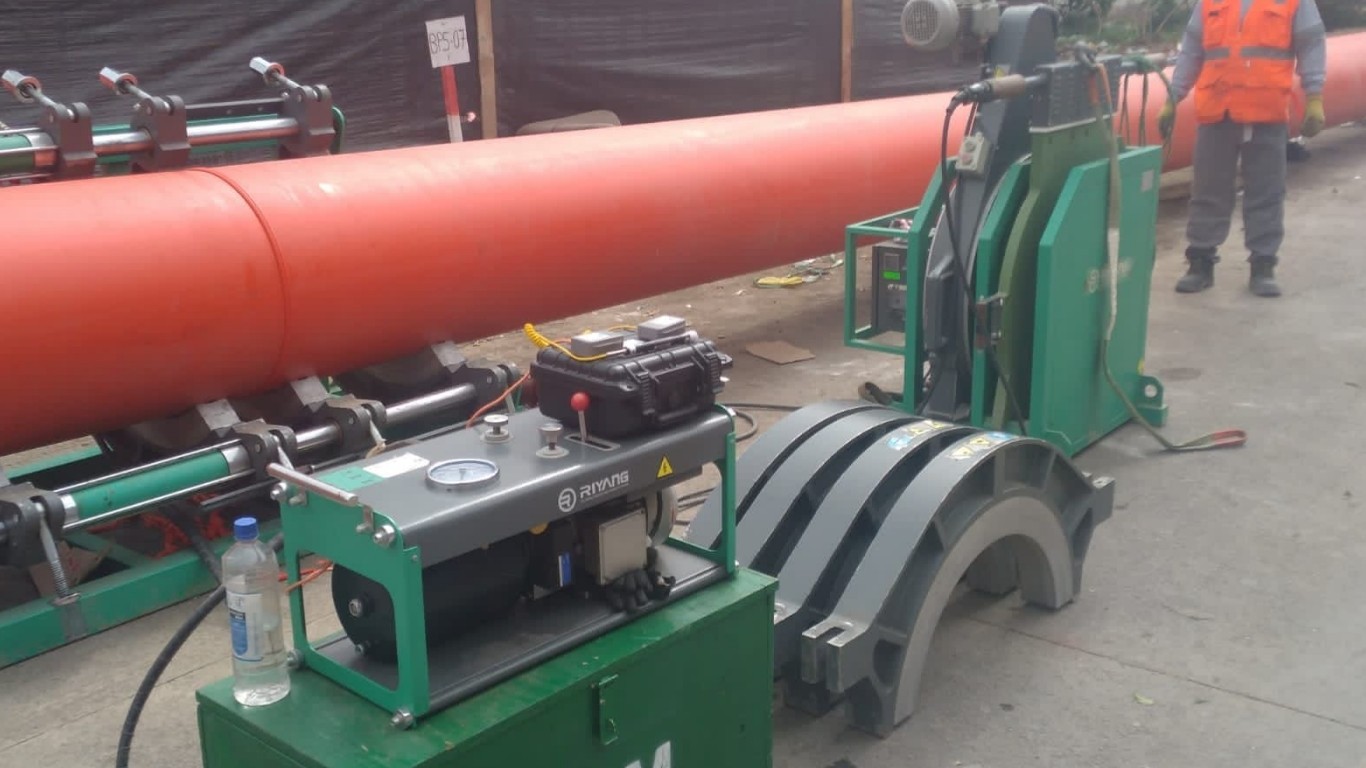
Pipe fusion machines weld plastic pipes and fittings. These machines are used to prepare and join thermoplastic polymer materials such as polypropylene, polyethylene, PVDF, and ECTFE pipes. A fusion splicer heats the ends of pipes and fittings and presses them together to form a pressure-tight, uniform joint, creating a continuous piping system that is as strong or stronger than the two fused parts.
Fusion welding technology
The three techniques for fusion welding thermoplastic pipes and fittings together are socket welding, butt welding, and electrofusion welding.
Socket fusion welding is used to assemble piping systems using injection-molded fittings. A metal socket mounted on the hot plate is used to heat the outer diameter of the pipe, while a metal sleeve on the other side of the hot plate heats the inner surface of the fitting. Once properly heated, remove the hot plate and push the pipe into the fitting.
Butt fusion welding is the end-to-end welding of thermoplastic pipes to form a continuous piping system. They are also used to manufacture custom fittings made from pipe material. During this process, a heating plate is inserted between the two tube ends. Press the pipe against the heating plate to allow the heat to seep into the pipe and soften the material. After the material has softened properly, the heating plate is removed, and the two pipe ends will be pressed together under the action of the butt fusion machine and held until sufficient cooling time has passed.
Electrofusion welding is the joining of thermoplastic pipes and fittings that have a built-in electric heating element around the area to be welded. When power is applied to the heating element, the heat generated melts the inside of the fitting and the outside of the pipe wall as the parts are held together. The components are then allowed to cool for the specified time.
Fusion welders are often adjusted to accommodate a range of different pipe diameters. The range of pipe sizes that a single fusion welder can handle is limited, so it is important to choose a machine that is suitable for welding pipes. Pipe fusion machines include rails and locks to ensure proper placement of pipes or fittings, as well as additional components to apply and maintain the correct force on both parts throughout the heating and cooling process.
Feature
Features available with different fusion welders include:
Working range from Ø 1" IPS ÷ 63" IPS (32mm to 1600mm)
Manual, hydraulic, or full CNC control
Capable of welding fittings such as elbows, tees, Y-branches, and short flanges
Power independent onboard generator
Powertrain and steering systems for self-propulsion
Wheeled trailer configuration
110 V and 230 V versions
milling cutter for cleaning welds
GPS traceability
Data logging function
The above briefly describes three fusion welding technologies, etc. If you want to buy a plastic welding machine, please contact us.
RIYANG is a professional custom thermoplastic welding machine manufacturer. We offer a wide range of products to meet the needs of field and workshop projects. Our products operate all over the world due to reliability, creativity and cost-effectiveness. At RIYANG, we are committed to making reliable machines for every application and making sure your choice is the right one.